Low Friction Coatings
Low friction coatings provide improved performance and service life while eliminating the need for wet lubricants in operating environments that require resistance to heat, chemicals, or clean room conditions. By reducing friction between two mating surfaces it's possible to extend the wear life of components. If the objective is to have a wear in period for the parts to size together, then a thicker coating solution might be required. If the application is an item with close tolerances or preload factors such as a bearing, then a very thin coating would be best to reduce friction. With years of experience and knowledge of applying low friction coatings to materials such as steel, aluminum, titanium, magnesium, carbon fiber, plastic, and rubber we help solve friction problems in a wide range of applications.
Low Friction Coating Selection Guide
- In addition to reducing friction, is corrosion protection also required?
- No: MSC recommends Tungsten Disulfide (WS2)
- Yes: MSC recommends Molybdenum Disulfide (MoS2) for when a thicker coating may be used.
- Is reduced friction needed with strong corrosion protection?
- Will there be heavy loads under pressure?
- For loads under pressure MSC recommends Tungsten Disulfide (WS2) which can withstand 100,000 psi or if a thicker coating is desired Molybdenum Disulfide (MoS2).
- Is a surface RA finish of less than 15 required?
- MSC recommends Tungsten Disulfide (WS2)
Low Friction Coating | Coefficient of Friction | Thickness (in.) | Cure Temperature | Operating Temperature |
---|---|---|---|---|
Tungsten Disulfide (WS2) | 0.035 | 0.00002" | Ambient | 1,200°F |
Nicklon (Nickel Teflon®) | 0.065 | 0.0002" - 0.002" | 200°F | 500°F |
Nicklon Plus (Nickel Teflon® Plus) | 0.065 | 0.0002 - 0.002" | 750°F | 500°F |
Molybdenum Disulfide (MoS2) | 0.07 | 0.0005" | Ambient to 400°F | 500°F |
Teflon® | 0.08 | 0.0006" - 0.0010" | 350°F - 715°F | 500°F |
Xylan® | 0.08 | 0.0006" - 0.0010" | 350°F - 715°F | 500°F |
- Tungsten Disulfide (WS2)
- Tungsten Disulfide (WS2) is a low friction dry lubricant coating that improves performance and service life better than other dry lubricants by reducing friction, improving mold release, and solving problems of excessive wear, seizing, galling and fretting. It is ideal for situations demanding close tolerances, high heat, and clean room conditions and was originally developed to eliminate galling of stainless steel on stainless steel, steel on steel or aluminum on aluminum and can take high loads & pressures. Because Tungsten Disulfide (WS2) is applied at ambient temperatures it can even be applied to materials such as carbon fiber that can not be heated to the temperatures required for PTFE application.
- Nicklon (Nickel Teflon®)
- Nicklon is a homogeneous distribution of autocatalytic nickel and PTFE and combines the benefits of reduced friction and increased corrosion resistance, making them perfect for rubber injection molds, there is a continual renewal of PTFE as the component surface sustains normal wear.
- Nicklon Plus (Nickel Teflon® Plus)
- Nicklon Plus takes the original Nicklon coating a step further by adding an additional low friction top coat that makes the coating harder.
- Molybdenum Disulfide (MoS2)
- Molybdenum disulfide (MoS2) is a dry film lubricant that prevents corrosion, galling, seizing and fretting to extend wear life when operating at temperatures between -350°F and +500°F and is suitable when a "wear in" period is necessary and a thicker coating is desired.
- Teflon®
- Teflon® PTFE non-stick coatings have a low coefficient of friction and temperature resistance up to 500°F. They also offer good abrasion and chemical resistance and can be applied to aluminum, carbon steel and stainless steel and address the low friction needs of engine components, compressors, pumps, and actuating devices.
- Xylan®
- Xylan is a dry film lubricant that is used on a number of surfaces to reduce friction even at high loads, prevent wear and galling, and provide additional lubrication. It is availible in a number of different formulations to best perform with the component requirement.
Test Results of Low Friction Coatings for Bearings & Gears to Improve Fuel, Battery & Engine Efficiency
Micro Surface partnered with a leading bearing manufacturer and testing facility to compare the performance of bearings coated with MSC's low friction Tungsten Disulfide (WS2) coating against an uncoated standard set of bearings. The first set tested was a Timken 2690 tapered roller bearing with Timken 2631 tapered roller bearing cup under the following protocols.
- Eight sets of stock bearings were purchased and half (4) were coated with Tungsten Disulfide (WS2).
- All bearings were lubricated with Aeroshell 22 high performance grease prior to testing.
- Bearings were installed in the test rig to undergo testing of increasing Axial and Radial loads at increasing speeds.
- Bearings were run through the testing protocols until excessive vibration was visible or temperatures reached 300°F.
The uncoated bearings made it through 4 hours of testing and failed due to high vibration after a few minutes into hour 4 while testing for the WS2 coated bearings stopped during measurements after 7.5 hours due to the temperature reaching 300F. The result of this testing showed that the Tungsten Disulfide (WS2) coated bearings lasted nearly twice as long and endured more rigorous testing conditions than the uncoated bearings while requiring a significantly lower level of torque and ran at a lower operating temperature. By reducing friction, the Tungsten Disulfide (WS2) coating enables the bearing to turn with a lower amount of torque required, resulting in a corresponding amount of energy being saved by requiring less power to turn the bearing. For electric motor and powertrain manufacturers this results in improved electric motor efficiency, increased mileage and a longer battery lifetime by reducing the number of charging cycles.
Elapsed Time (hr) | Speed (RPM) | Axial Load | Radial Load | Coated Torque | Uncoated Torque | Coated Temp (F) | Uncoated Temp (F) |
---|---|---|---|---|---|---|---|
0.5 | 1,500 | 325 | 1,250 | 11.34 | 16.22 | 86.11 | 80.37 |
1.0 | 2,250 | 8.84 | 14.69 | 110.09 | 110.03 | ||
1.5 | 3,000 | 6.96 | 16.13 | 110.19 | 136.52 | ||
2.0 | 750 | 650 | 2,500 | 15.06 | 19.08 | 121.05 | 155.16 |
2.5 | 1,500 | 8.58 | 17.58 | 99.35 | 112.88 | ||
3.0 | 2,250 | 9.19 | 41.25 | 116.29 | 132.05 | ||
3.5 | 3,000 | 7.13 | 20.94 | 122.03 | 221.53 | ||
4.0 | 750 | 975 | 3,750 | 11.91 | 34.26 | 74.15 | 67.54 |
4.5 | 1,500 | 12.14 | Fail | 96.16 | Fail | ||
5.0 | 2,250 | 11.58 | Fail | 116.28 | Fail | ||
5.5 | 3,000 | 13.88 | Fail | 116.47 | Fail | ||
6.0 | 750 | 1,300 | 5,000 | 37.63 | Fail | 187.79 | Fail |
6.5 | 1,500 | 24.76 | Fail | 144.53 | Fail | ||
7.0 | 2,250 | 29.31 | Fail | 192.25 | Fail |
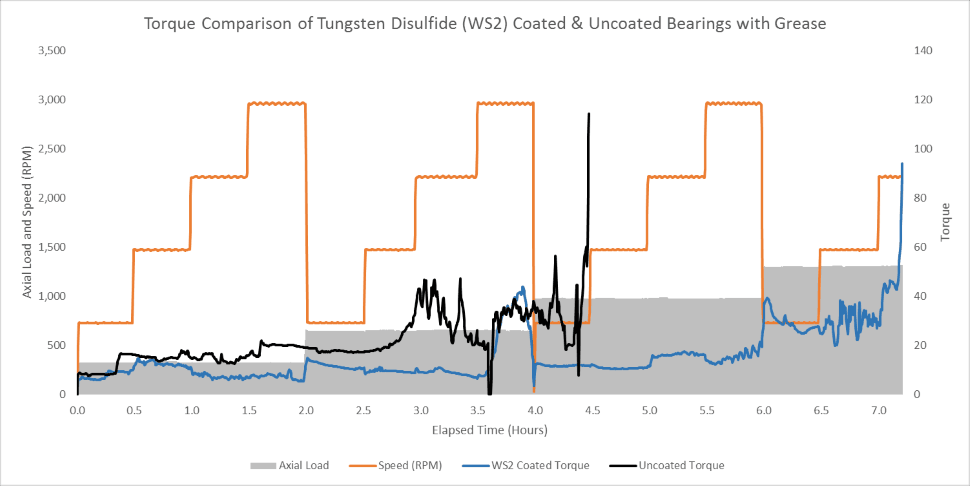
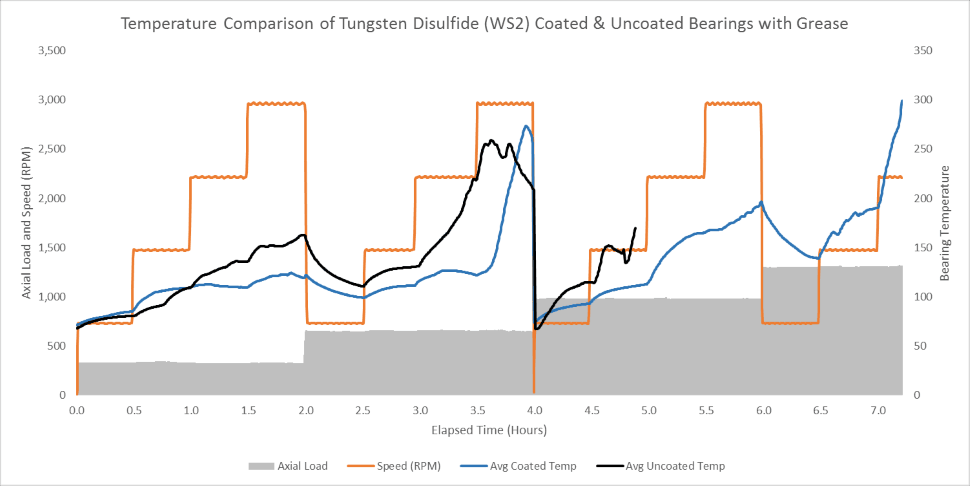
According to the U.S. Department of Energy, a third of an automobiles fuel or electric energy consumption is spent overcoming friction which has a direct impact on emissions and miles per gallon (MPG) or Miles per gasoline equivalent (MPGe). However, by coating components of a car with a coating like Tungsten Disulfide WS2, it is possible to reduce the friction on the rubbing and turning of various mechanical parts in the engine, transmission, and exhaust systems such as gears, bearings, pistons, and shafts and as a result improve fuel or energy consumption and emissions and lower CO2 emissions.
Although adding a low friction coating adds an additional initial expense to the cost of a component, the long term benefits that are realized far outweigh this by reducing energy consumption which saves money and fuel or battery power and also allowing production to continue for an extended period.
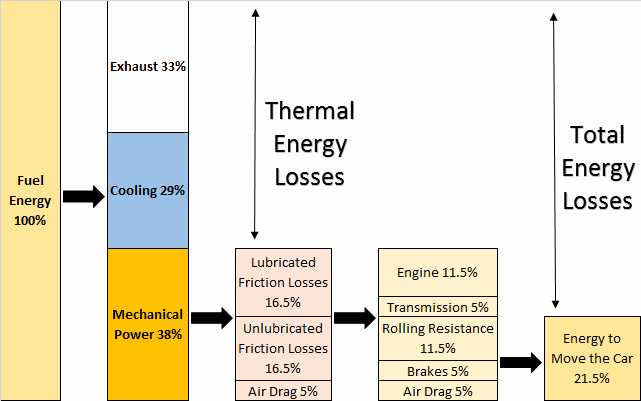
Energy Output | Energy Consumed % |
---|---|
Exhaust | 33% |
Cooling | 29% |
Mechanical Power | |
Engine | 11.5% |
Transmission | 5% |
Rolling Resistance | 11.5% |
Brakes | 5% |
Air Drag | 5% |
Component with Friction Problem | Recommended Low Friction Coating |
---|---|
ABS rings | Xylan 1010 |
Rotors | Xylan 1010 |
Bearings | Tungsten Disulfide (WS2) |
Blowers | Xylan 1010 |
Cam rings | Xylan 1331 |
Connecting rods | Tungsten Disulfide (WS2) |
Exhaust systems | Xylan 1010 |
Fan drives | Xylan 1014 |
Fasteners | Xylan 1424 |
Injector-pump cam rings | Xylan 1331 |
Lock mechanisms | Tungsten Disulfide (WS2) |
Noise reduction | Tungsten Disulfide (WS2) |
Piston rings | Tungsten Disulfide (WS2) |
Seat-belt clips | Xylan 1052 |
Seat tracks | Xylan 1014 |
Sleeve bearings | Tungsten Disulfide (WS2) |
Turbocharger parts | Tungsten Disulfide (WS2) |
Valves | Tungsten Disulfide (WS2) |
Air Cylinder Pistons | MoS2 |
Hinges | Xylan 1010 |
Sliding Bearings | Tungsten Disulfide (WS2) |
Actuators | Xylan 1010 |
Ball Valves | Xylan 1010 |
Cams | Tungsten Disulfide (WS2) |
Chutes | Xylan 1010 |
Carburetor Shafts | Tungsten Disulfide (WS2) |
Carburetor Throats | Xylan 1010 |
Fan Blades | Xylan 1010 |
Gears | Tungsten Disulfide (WS2) |
Guides | Xylan 1010 |
Platens | Xylan 1010 |
Pistons | Tungsten Disulfide (WS2) |
Pneumatic Components | Tungsten Disulfide (WS2) |
Shafts | Tungsten Disulfide (WS2) |
Automotive | Tungsten Disulfide (WS2) |
Aerospace | Tungsten Disulfide (WS2) |
Defense | Tungsten Disulfide (WS2) |
Plastic Tooling | Tungsten Disulfide (WS2) |
Release for Plastic Molding | Tungsten Disulfide (WS2) |
Bearing Dry Lubication | Tungsten Disulfide (WS2) |
Industrial | Tungsten Disulfide (WS2) |
Industrial Corrosion | Nicklon |
Long Wear Life for Automotive & Defense Department/Military | Tungsten Disulfide (WS2) |
Components that require additional Corrosion Protection | MoS2 |
Components that require additional Chemical Resistance | MoS2 |